Battery Cooling Air Filter for Hybrid Buses
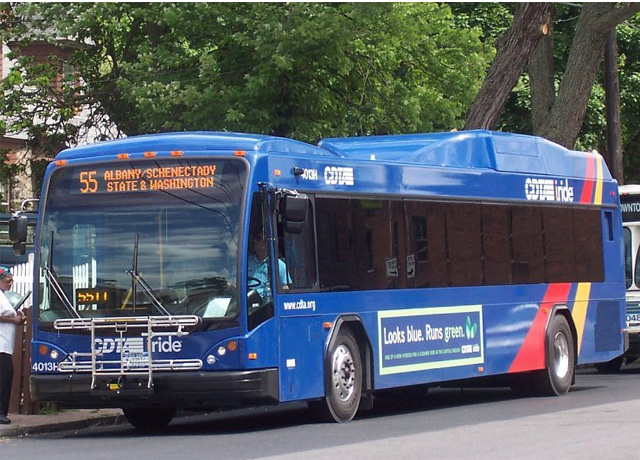
Industry: Commercial & Transit Vehicles
Application: Hybrid Bus Battery Pack Inlet Filter
A Tier 1 battery manufacturer required a higher performance air filter to the current filter used to filter cooling air entering a roof mounted battery pack for Hybrid transit buses. They needed a cartridge/panel style filter with the ability to quantifiably capture 85% of 0.5 micron particles with a 0.22″ pressure drop across the filter and they needed prototype samples for testing within two weeks.
APC required a $5000 retainer to cover engineering time, proto-type filter development and testing costs. Any remaining funds would be used towards filter production after filter testing and pre-production QC sample approvals.
APC manufactured two different prototype filter samples within 7 days for client testing. Based on their feedback, a third prototype filter was made to fine-tune filter efficiency, pressure drop, and operational temperature requirements. Initial filter testing and prototype filter submission was all completed within a 4 week timeframe.
The next phase required 20 prototype filters for 6 month field testing:
- Test 1: New York City. Wintertime testing subjected the filters to sub zero temperatures, wind, snow, sleet, ice, and road salt.
- Test 2: Arizona. Filters subjected to superfine Arizona road dust, below 0.5 micron, and high operating temperatures.
- Test 3: California. Filters subjected to sea salt spray, heat, battery draw and stress from steep roads.
All three tests challenged the filters’ air cooling and filtration capabilities to keep battery cells clean and operating temperatures in check to maximize battery performance.
To learn more about this hybrid bus battery pack inlet filter project, or about our other products and services, please contact APC Filtration, Inc.